Ruggedized Cable Solutions for Harsh Environments
Ruggedized Cable Solutions for Harsh Environments
Many applications from a variety of industries need to perform in harsh environments, such as extreme temperatures, exposure to chemicals, or demanding applications that repeatedly flex like a robotic arm. Ruggedize your cable with the right material selections and components for reliable performance.
From conductor materials and stranding configuration, to strength members, shielding, and even jacket materials, this article will outline a few of these choices We recommend involving a cable design engineer early on in your project to assist with recommendations to meet your specific end application performance goals.
Conductor Materials
The conductor materials are at the core of the cable to power, communicate, and control devices. Conductor materials and the stranding design of the conductor play a large role in reliability and performance.
Bare copper
Bare copper is the most commonly used conductor type and is preferred in most applications because it is highly conductive and very cost effective. Offering a pure signal over long distances, bare copper also has natural flexibility and high tensile strength.
Tin-plated
If the custom cable or cable assembly will be used in a wet environment and corrosion resistance is a requirement, then tin-plated copper is a good conductor option. Another cost-effective solution, tin plating is also easy to solder and can withstand up to 150°C.
Nickel-plated
Nickle-plated copper is often used in high temperature applications due to its ability to withstand up to 450°C. In addition, the nickel plating offers corrosion and wear resistance.
Alloys
Alloys are a combination of 2 or more metals. Silver, nickel, copper, beryllium, cadmium, RoHS-compliant chromium are selected for their overall toughness, break strength, and flex-life. Alloys are another great option for high temperature applications.
Steel
Steel is not a great conductor unless coated, but it is extremely strong and has less stretch than other conductor materials. Due to its high tensile strength and crush resistance, steel is often used in military and aerospace/defense applications.
Stranding Designs
Stranding configuration selection, like any cable component, depends on the end-application of the cable and the environment in which the cable must perform. Key deciding factors are flex and movement requirements of that application. The typical rule of thumb for ruggedizing your conductor from a stranding perspective, is “the more strands, the more flexible and the longer the lifespan”.
Rope Lay
By far the most flexible construction from a movement and motion standpoint because it maintains a tight diameter while also allowing for a larger number of fine strands to be used.
Bunched
This type of stranding offers flexibility at a lower cost, although it will not have as high of a flex life as rope lay. This configuration is basically a ‘bunch’ of strands gathered together in no particular arrangement.
Concentric
Each layer of stranding has the opposite lay direction, resulting in an increased lay length with each layer. This is another great option for flex applications especially with torsional demands.
Tubing
Adding tubing to your cable design may be done for a number of reasons including to supply, vacuum or vent. Depending on the application and environment, it might be supplying liquid, vacuuming gas, dissipating heat, pressure, or even steam. A cable designer will pay close attention to the end application when selecting the best material to ensure the tube doesn’t get bent or collapse under pressure if being used in a rugged environment. It is also important to think about the termination of the cable when selecting tube materials because over molding, for example, can compromise the integrity of the tube as a result of the pressure applied during assembly.
Strength Members
Add support to preserve cable integrity and help the cable withstand different types of movement with a strength member.
Aramid fiber is a strong material ideal for extreme pulling strength.
Steel strength members may be a better choice if pull strength and compressive strength are critical.
A fiberglass rod offers rigidity, when designing for a pulling or pushing application.
When designing a strength member into a cable assembly, be sure to keep in mind which connector will be used and how the strength member will be terminated. There are a couple of different ways to terminate the strength member depending on its function within the cable.
Separator
Separators serve as barriers between the cable’s core components and the outer jacket material so that they do not bond together. Flex facilitating tapes such as PTFE or spun nylon will help increase both flexibility and flex life. These tapes can be wrapped in-line with jacketing and will help the cable flex without compromising the structure of the cable. It will also protect the cable from repeated flexing in a demanding, high flex life application.
Water Blocking
Unlike other cable manufacturers, which use a jelly filler as a barrier for the first few inches of the cable, Northwire implements a dry component throughout the entire length of the cable that only activates when wet. Highly effective in preventing and mitigating leaks, this unique alternative also allows for a much more convenient and cleaner process when installing and handling the cable.
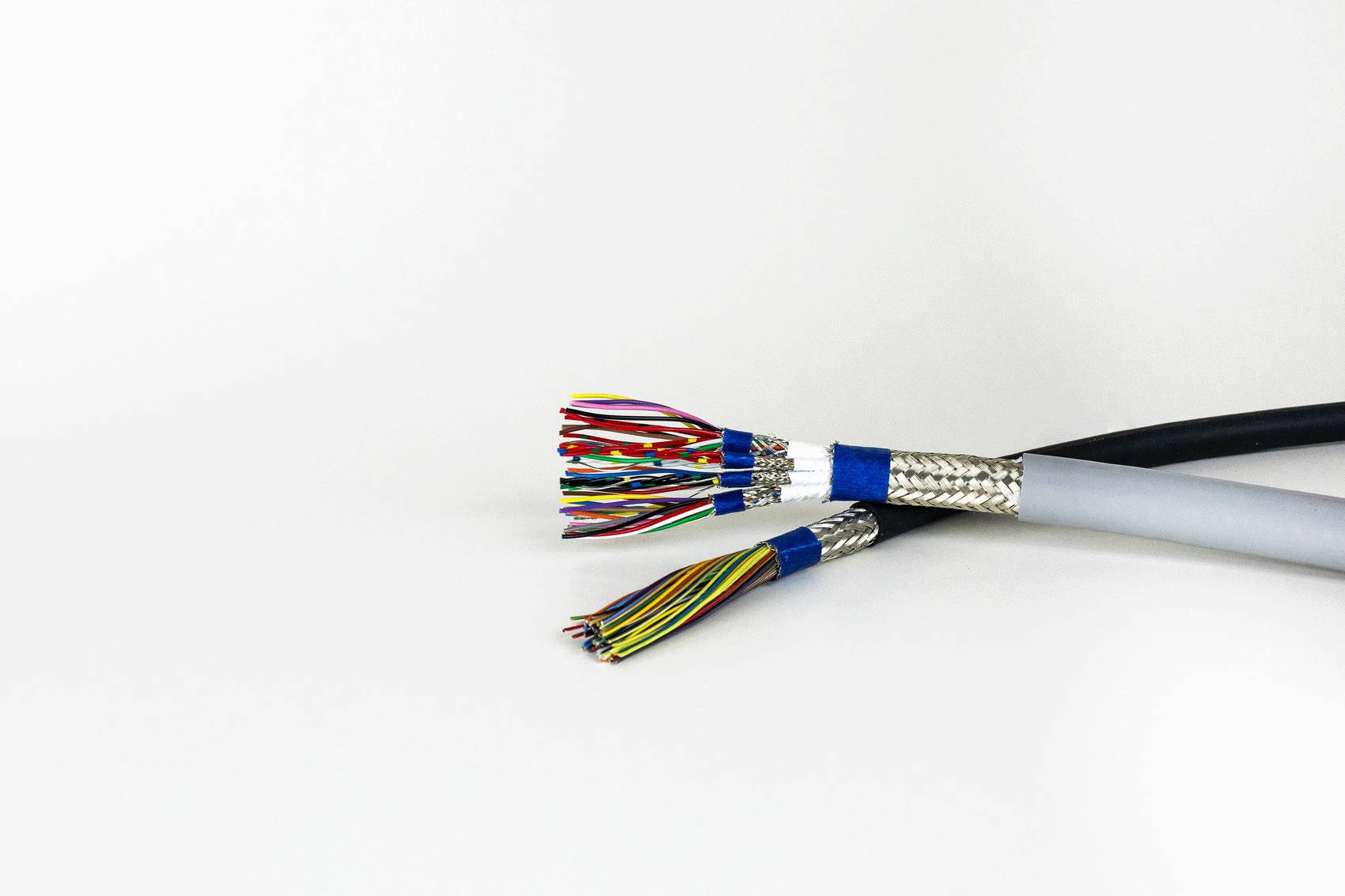
Shielding
Shielding provides protection to cable and wire by increasing both structural integrity and signal integrity. The primary types of cable shields include a foil shield, a box weave or basket weave braid shield, and a spiral shield. Selecting the right shielding materials and configurations can add strength, flexibility, and noise suppression.
Foil
A foil shield is a cost-effective option that is also lightweight and flexible. It will reduce cross-talk while protecting inner components and/or the entire core depending on how it is designed into the cable.
Braid
A braided shield offers superior structural integrity & physical protection along with a higher flex life. The increased mechanical strength does come with a trade-off as the braid will be more costly and a little more difficult to terminate. This type of shield does reduce cross-talk and protects against EMI.
Shielding to Reduce Interference
The most effective shielding against interference is a combination of braid and foil shields. From an electrical standpoint, foil will guard against high frequency noise and a braid will guard against low frequency noise. A combination of the two is ideal for maintaining signal integrity.
Shielding to Increase Flex Life
Foil provides a layer of shielding without adding a lot of weight or cost, but when high flex life is required, it may not be the best material. A spiral shield provides more flexibility, but may have a shorter life span in high flex environments. A box weave, while stiffer, will stay together throughout the flex life of the application due to its interlocking nature.
Shielding to Act as a Barrier
Tapes, wraps, and separators serve as barriers between a cable’s core components and the outer jacket material so that they do not bond together. Shields protect the integrity of the stranding and increase the resistance to damage, noise, and moisture.
Each type of material and type of braid brings different properties and strengths to the table. Once you understand what you need in your shielding, find the right material and structure for the job. Configurations to isolate and separate internal components are very customizable.
Retractiles for Rugged, High Flex Life Applications
If the cable will be used on a robotic arm or a security camera where torsional and rotational movement puts demands on the flex life of the cable, a retractile may be your best option as the coil will relieve much of the stress that would otherwise be placed directly on the inner conductors.
Jacketing
Jacketing is the first line of defense, it protects against environmental factors and application demands. Each jacket material offers different properties and special material blends can be compounded to meet performance needs. An application engineer will work closely with you to identify the best jacket solution, for example:
Fluoropolymers are excellent for withstanding extreme temperatures as well as cut, crush, and/or abrasion resistance as the material maintains rigidity even in high temperatures
TPU (Thermoplastic Urethane) is a good option in abusive environments where chemical resistance is needed. It is also an excellent choice for a retractile cord
TPE (Thermoplastic Elastomer) may be considered if flexibility is important. It is a softer alternative which maintains strength and damage resistance making it a good option for coil cords as well
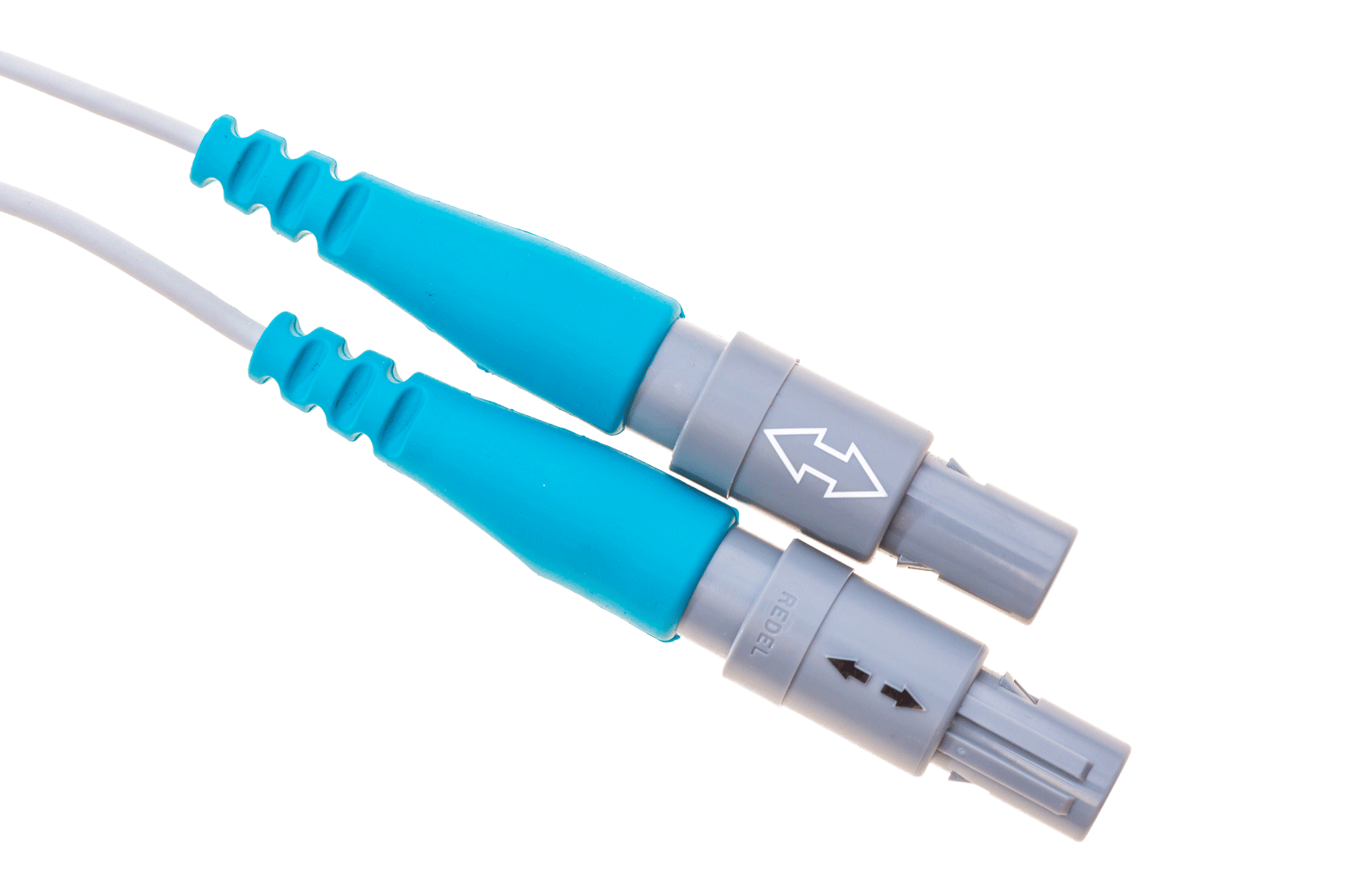
Over-molding
There are many options when it comes to terminating your cable to a connector especially when flex is a critical factor. An over-molded strain relief is going to give your assembly a much longer flex life than a boot. The over-mold will offer added protection from flexing near the connector or pulling that might occur from flex demands further down the cable. Additionally, a service loop inside the connector will offer a buffer, so that any pull on the cable will not immediately pull the conductors out of the pins.
As you can see, there are several ways to ruggedize your cable for performance in harsh environments. The types of materials chosen and the components utilized will be dependent on the needs of the specific end application and the demands placed on the cable or assembly in its working environment.