Optimize your Cable for Flexibility and High Flex Life
Optimize Your Cable for Flexibility and High Flex Life
Cable types include terms like “flex,” “flexibility,” and “flex life”. What factors affect or influence flex? What are the best material options to make a cable solution more flexible or maintain a longer flex life?
Understanding the flex requirements of an application is crucial before selecting the wire and cable material and components. Knowing how many cable systems are required to tolerate movement – whether small movements during initial installation or daily repetitive movements.
Within the world of “flex,” flexibility and flex life may sound equivalent, but there are key differences. In fact, some high flex cables can have short flex lives, and other wires and cables with high flex life may not be particularly flexible. Let's take a look.
Flexibility
Simply put, flexibility is a measure of how much movement a cable can tolerate at a given time. Flexibility types include: torsional, rolling, bending, and variable. When a cable is bent, twisted, or pulled into positions beyond its original state, its flexibility is tested.
Flexible cable can bend significantly and stay bent for a large amount of time without being damaged.
If your cable needs to bend or curve around infrastructure, you may need high flex cable, or cable with strong flexibility.
Flexible cable is also referred to as ‘supple’. Flexible cables are soft, supple, and easy to manipulate or bend back and forth. Think of a surgeon using an electrosurgical tool. With this application, the surgeon needs supple, flexible cable to easily manipulate the tool. Cable kinking, back twisting or pulling on the surgeon’s hand would result in fatigue and less surgical precision.
Flex Life
Flex life deals with how often a cable moves without becoming damaged. Many cables can bend for limited use, such as during installation. High flex life cable bends repeatedly and routinely without disrupting the cable’s intended use. Examples include power supply cables, data transfer cables, and robotic application cables.
Ultimately, if your cable needs to move well, it must be flexible. If your cable needs to move often, it must have a high flex life. In many applications, such as industrial machinery or factory automation, both flexibility and high flex life are required.
Within flexibility and flex life are movement variations to consider within your end application.
- Retractable. A coiled or spiral cable is intended to “snap back” into shape after being pulled or extended.
- Torsional. When a cable is twisted, pulled, or rolled around its axis, it experiences torsional flex.
- C track, Drag chain, or Rolling. Often seen in track systems, rolling a cable not only stresses the cable’s interior components, but also wears down the outer jacket over time.
- Variable. More “free form,” variable flex may make a cable move on multiple points in multiple directions – often seen in robotics.
- Bending. This “tic toc” motion often happens when part of the cable is stationary, and the other part is bent back and forth over a fixed object.
- Continuous. In many industrial applications, flex isn’t occasional – the cable may be part of equipment that requires constant, repeated movement for the lifespan of the system.
Repetitive Flexing and Material Selection
Repetitive flexing can cause serious damage to wire and cable systems. Internal conductors may break, outer jackets can erode or tear, and friction can cause overheating. Not only does this decrease the lifespan of the cable, it can cause system downtime or damage.
System downtime or damage can be avoided by selecting the right cable materials and components for optimal flex characteristics. Material choices in a variety of components can help increase flexibility or extend flex life for your end application. These include stranding, conductor insulation, braid, strength members, jacketing and more.
Stranding
For a high flex cable, choose a high strand count. Typically, the more strands, the more flexible and the longer the lifespan of the cable.
For movement and motion, a rope lay stranding construction is the most flexible configuration. It is also the most expensive. These are the trade-offs to consider when choosing materials. With the rope lay configuration, there are a number of individual bundles of stranding twisted into groups that make up one larger, solid configuration.
When aiming to achieve a high flex life, concentric stranding is a better choice. In a concentric strand, there is a solid conductor running down the center that is surrounded by layers of rotating strands. Each layer is comprised of strands running the same direction, but the direction alternates for each layer.
Insulation and Jacketing
When selecting insulation and jacketing materials, choose materials with a high dielectric strength. A higher dielectric strength means a thinner wall can be extruded for less material in the way, making it more flexible.
Choose a ‘soft’ material with a ‘shore a’ durometer of 80 or lower. The softer the cable, the easier it will be to bend and flex. A thinner wall and softer material will increase the cable’s suppleness.
Strength Members
Strength Members include steel, aramid fiber, or a stiff fiberglass rod that extends the center of the cable.
Strength members offer many benefits to the cable:
- Adds support to preserve cable integrity
- Adds function and protection
- Helps the cable withstand movement types including:
- Pulling
- Torsion
- Continuous
- Variable
- Bending
- Rolling
Aramid fiber, such as Kevlar® is a strong material ideal for extreme pulling strength while maintaining flexibility and flex life. Aramid fiber can be stranded in a variety of configurations to achieve differing levels of strength. For example, a bundle of four strands provides 450-600 Newtons of pull strength. While it is not rigid, it does offer high compressive strength without adding significant weight.
If aramid fiber is used in a cable solution, special attention must be given to the cable’s termination, as incorrect termination can lead to weak points in the fiber. We have even seen cases where a customer comes to us with a competitor’s cable assembly that is failing in the field because the strength member was never terminated, so it was not being put to use.
Separator
Separators serve as barriers between the cable’s core components and the outer jacket material so that they do not bond together. Flex facilitating tapes such as PTFE or spun nylon will help increase both flexibility and flex life. These tapes can be wrapped in-line with jacketing and will help the cable flex without compromising the structure of the cable. It will also protect the cable from repeated flexing in a demanding, high flex life application.
Shielding
Shielding provides protection by increasing both structural integrity and signal integrity. Selecting the right shielding materials and configurations can add strength, flexibility, and noise suppression. The primary types of shields include a foil shield, a box weave or basket weave braid shield, and a spiral shield. Foil provides a layer of shielding without adding a lot of weight or cost, but when high flex life is required, it may not be the best material. A spiral shield provides more flexibility, but may have a shorter life span in high flex environments. A box weave braid, while stiffer, will stay together throughout the flex life of the application due to its interlocking nature.
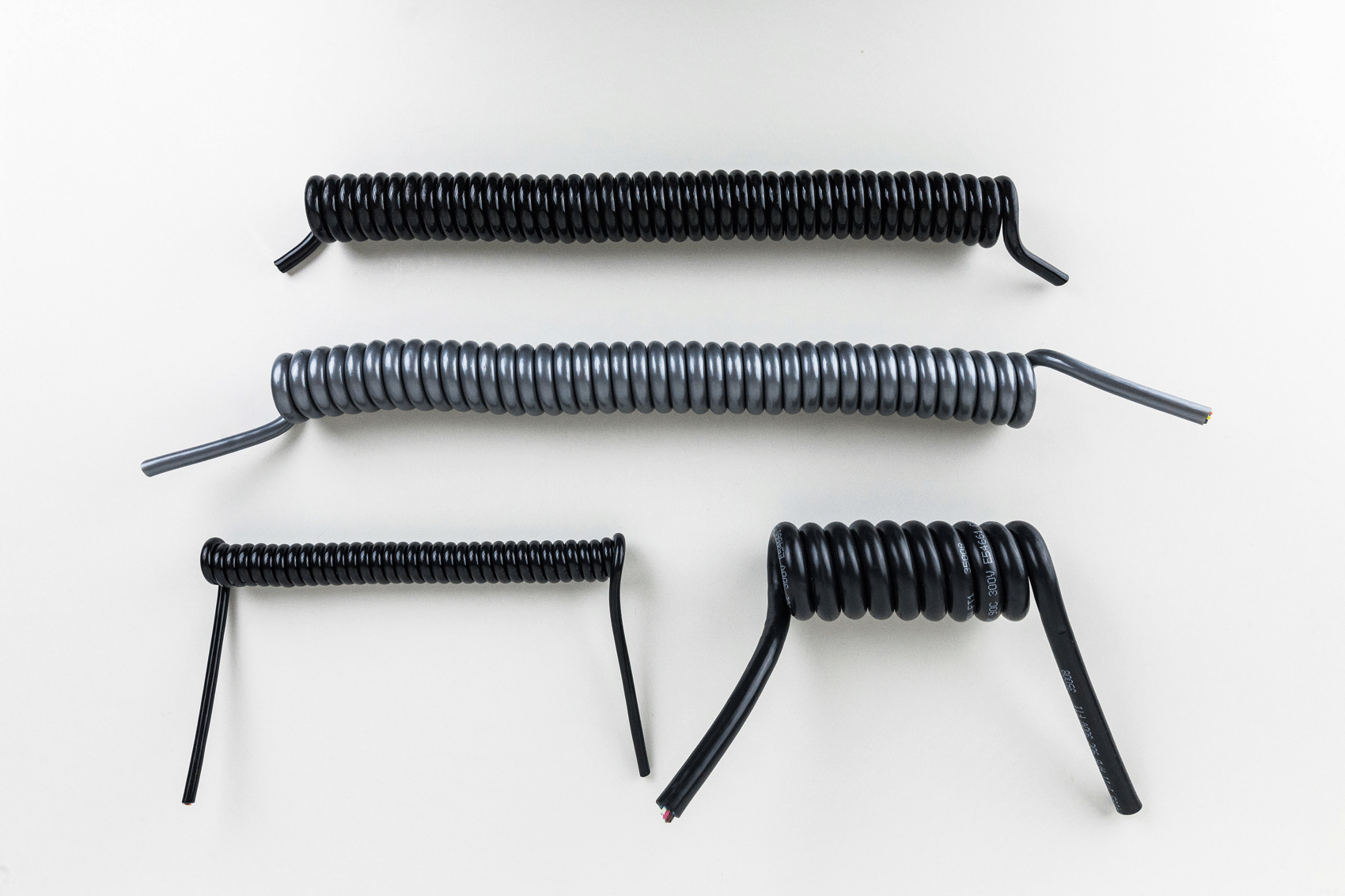
Retractile
A retractile coil cord can also be beneficial when flexibility or high flex life is required. If the cable will be used on a robotic arm or a security camera where torsional and rotational movement puts demands on the flex life of the cable, a retractile may be your best option as the coil will relieve much of the stress.
Assembly
There are many options when it comes to terminating your cable to a connector especially when flex is a critical factor. An over-molded strain relief is going to give your assembly a much longer flex life than a boot. The over-mold will offer added protection from flexing near the connector or pulling that might occur from flex demands further down the cable. Additionally, a service loop inside the connector will offer a buffer, so that any pull on the cable will not immediately pull the conductors out of the pins.
Hopefully this article has you thinking about the requirements of your cable and different material options that may improve its performance. As you have probably gathered, flex, flexibility, and suppleness can be interpreted differently, so it is important to understand the needs of the end application to ensure a properly designed cable and assembly solution.
Additionally, if your current cable is underperforming, it is important to understand what is failing and where, so a cable designer can select the right materials to rectify the situation.