Custom Cable Options: Tapes, Wraps, and Fillers
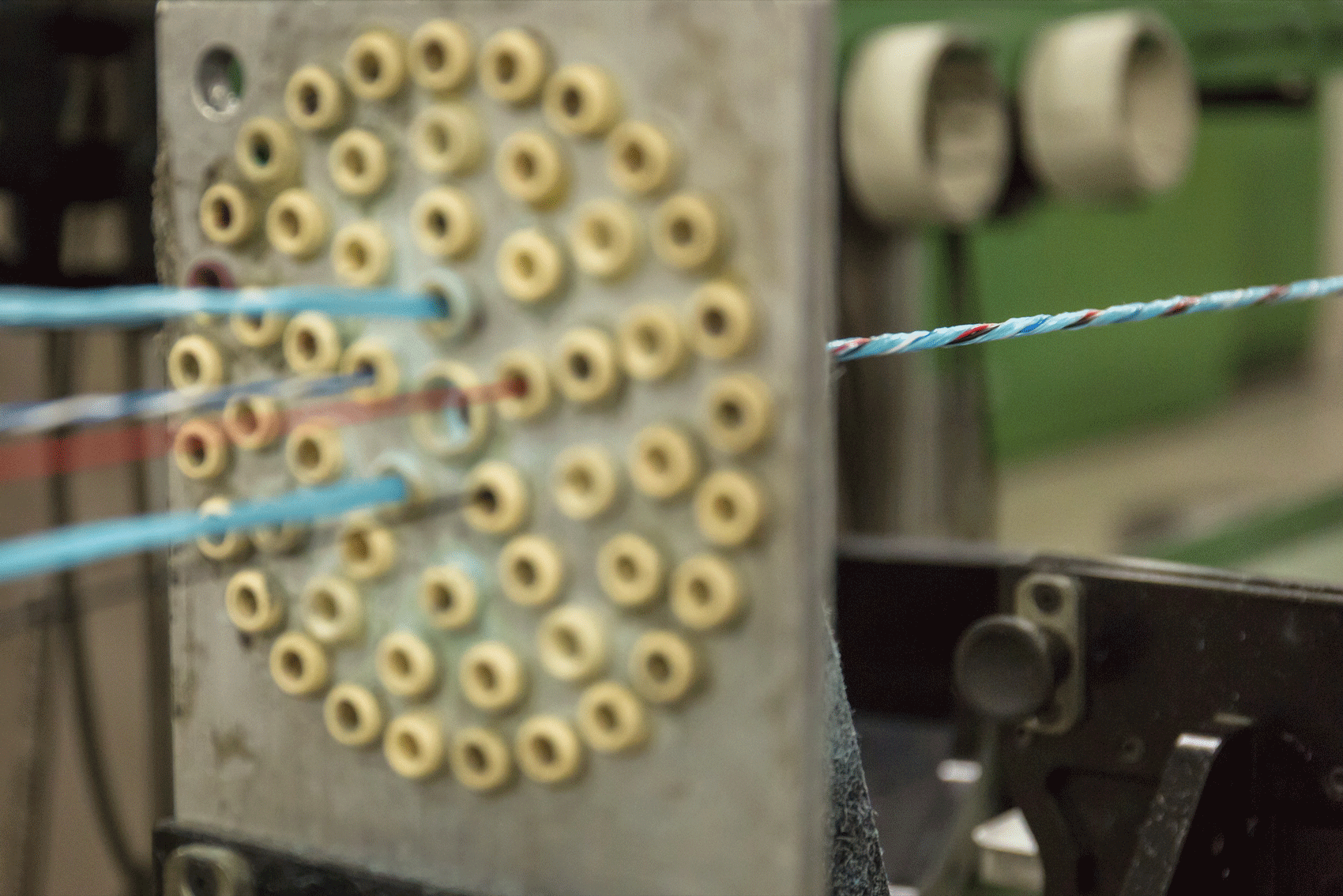
Does your cable need increased flex life? Will your cable need to perform in extreme temperatures? Worried about cross-talk?
The addition of tapes, wraps, and fillers to your custom cable design can address concerns about your cable flex life, performance in extreme temperatures, and cancel cross talk.
Benefits of using tapes and wraps within your custom cable:
- Offers noise suppression or elimination of cross-talk between inner components
- Adds shielding and isolation
Tape and Filler Material
Many tape and filler options are available. Material options can be applied at various operations to achieve a range of functions.
Commonly used tape materials:
Paper
- Separator between core and jacket
- Light weight and flexible
- Least expensive
Mylar (polyester)
- Binds components or entire cable
- Opaque, clear, or aluminized
- Cost effective
- Less flexible
Spun Nylon
- More flexible
- Light weight
- More expensive
PTFE
- Most expensive
- Superior flexibility
- Chemical
Filler Benefits:
- Fills in gaps to make a cable round and more aesthetically appealing
- Increases flex life depending on coverage and material used
- Protects from moisture and chemicals
- Makes it easier to mold and seal in glands
- Options are available for water blocking
Filler Materials:
- Polyolefin
- Cotton
- Extruded thermoplastics
- Paper
- Strings and yarns
Learn more about tapes, wraps and fillers by downloading the Extreme Materials White Paper.
Need more than one function in your tape, wrap, or filler? Customizable and coverage can range from full to minimal depending on your needs. If a long flex life, insulation, moisture protection, or extreme temperature consideration is something your cable needs, a tape, wrap or filler might be a good addition to your custom cable design.