Custom Cable Assembly Series: Soldering vs Crimping
Posted On:
July 11, 2018
What makes the best termination: solder joints or crimp connection?
When you hear one over the other it is normally based on preferences, not performance. Both methods will produce highly reliable wire terminations when processed correctly.
For building cable assemblies, it is simply a matter of choice. Prototyping leans toward soldering because of the low cost of entry and re-workability. Whereas high-volume production leans toward crimping with its controllable process and easy learning curve, resulting in lower labor costs.
Here's a helpful list of pros and cons:
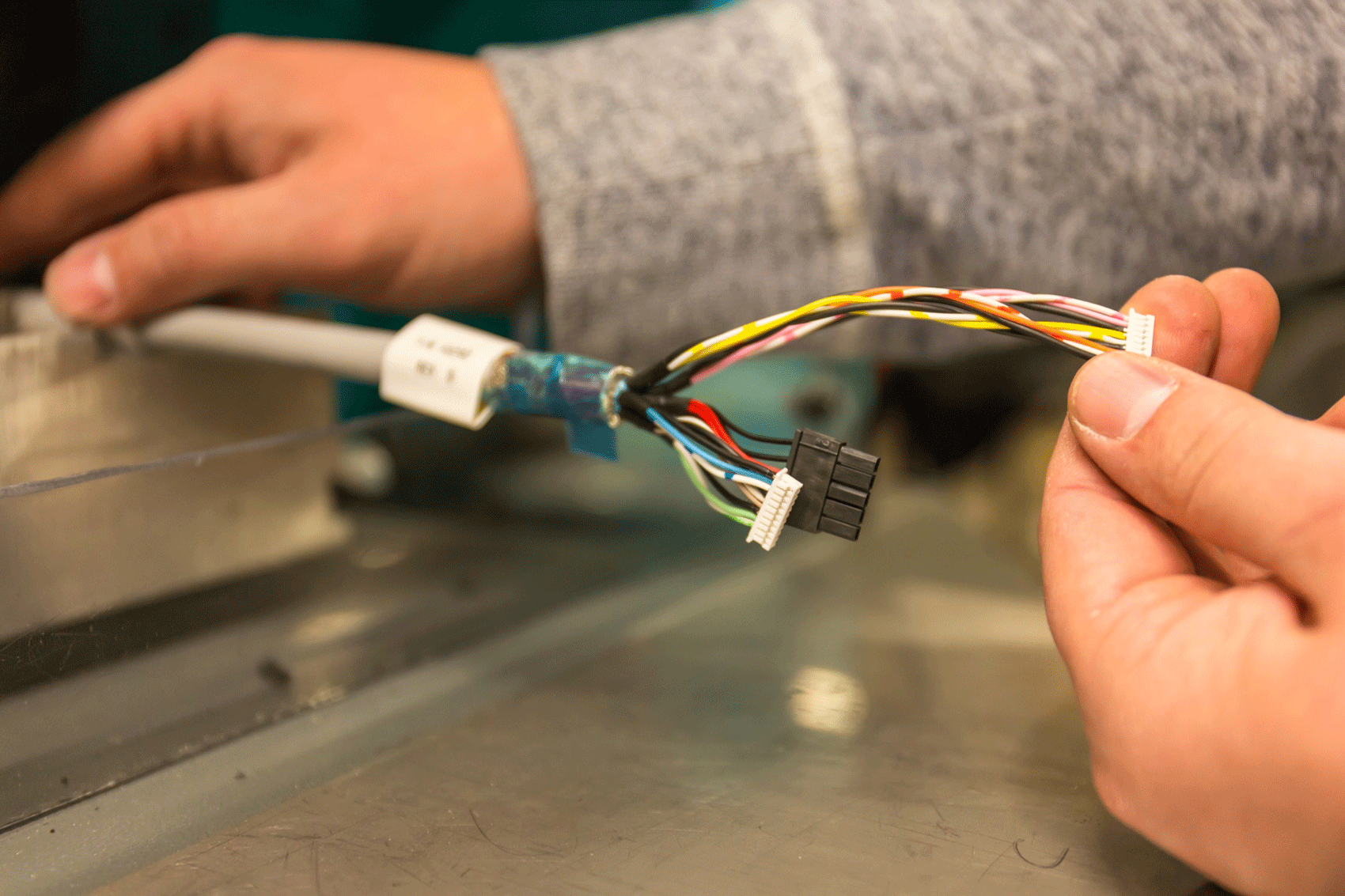
Crimping Terminations
PROS
- Easy learning curve
- Controllable process. e. Crimp height control charts
- Gas tight termination
- Faster termination - easier to automate
- Good for both high and low volumes
CONS
- Higher cost of entry
- Low flexibility - due to the need for exact wire and terminal size matching
- Difficult to re-work
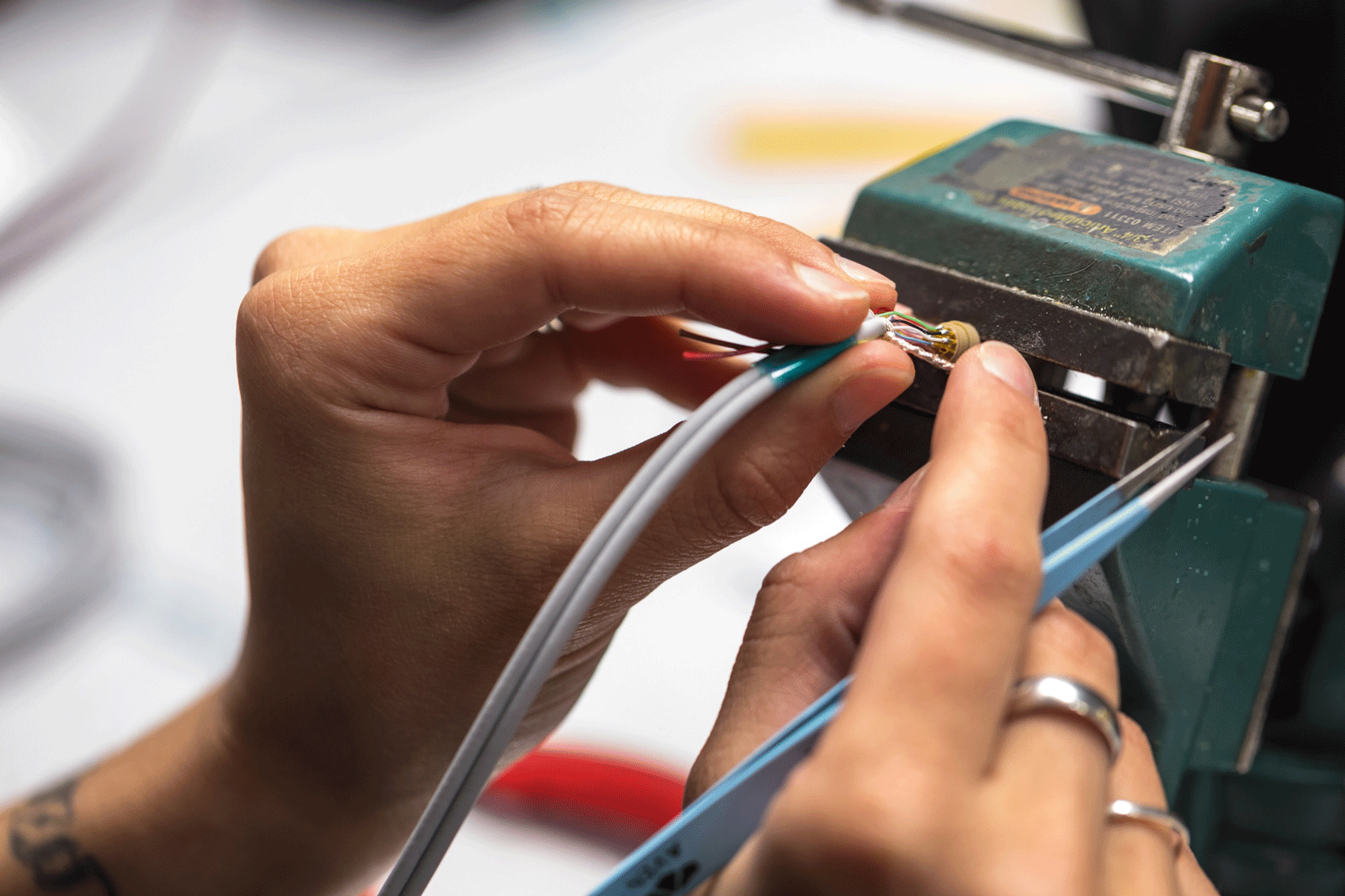
Solder Terminations
PROS
- Low cost of entry
- Flexibility - wire gauge and terminals do not need to match exactly
- Easily re-workable
CONS
- Requires a skilled workforce, inexperience can lead to wire and conductor damage
- Non-controllable process
- Difficult to determine a bad solder joint
- Not suited for high volume production
- Flux contamination leading to electrical issues
Do you have a custom cable assembly? Let us help!
Request a Quote!