Like many of the best discoveries, the first fluoropolymer, polytetrafluoroethylene or PTFE, was discovered by accident when DuPont chemist Dr. Roy Plunket was working with fluorocarbon refrigerant gasses. When Dr. Plunket went to open one of the gas cylinders, no gas came out. Instead, a white waxy solid that did not melt or dissolve was found inside which would come to be known as PTFE or Teflon®.
Historically, PTFE has not been melt processable. Ram extrusion has been the most common way to process the material in the wire and cable industry. This process takes PTFE in a powder form and gravity feeds it into a chamber. A hydraulic ram pushes the resin from the chamber to the die. The downside to this process is that you are limited on the length of material you can process, and the thickness can be very inconsistent. These limitations are what motivated Northwire to offer a better solution and an extrudable PTFE that can be processed with a traditional screw extruder, which results in no length restrictions and a very uniform wall thickness in terms of cable insulation. More on that later…
Since the discovery of PTFE, many additional fluoropolymers have been discovered, which has mainly been driven by the need for an extrudable or melt processable PTFE. There are several fluoropolymer material options on the market, here are some of the most common in the cable and wire industry:
PTFE
- The most fluorinated of all of the fluoropolymers, resulting in superior performance in terms of resistance to extreme temperatures, chemicals, oils, solvents, cut, crush, and abrasion
- The main downside to PTFE has been the fact that this material has to be ram extruded, which means there are length restrictions based on how much resin can fit into the chamber
PFA
- PFA is the closest to PTFE in terms of superior performance characteristics
- One trade-off for the high-performance characteristics is the price
FEP
- The first melt processable fluoropolymer to be released
- FEP does not have the almost universal chemical resistance featured by PTFE and PFA, but does offer a more cost-effective alternative to PFA where these two characteristics are not as imperative
ETFE
- Features improved cold flow resistance, higher tensile strengths, and increased abrasion resistance
- Although not fully fluorinated like the 3 above, ETFE maintains high temperature performance, very good electrical properties, and chemical inertness
Why do people use fluoropolymers as a cable insulation or jacket material? These materials are requested for a variety of reasons, but here are the main Features and Benefits of Fluoropolymers:
• Extreme temperature resistance, -200°C to 260°C
- Up to 300°C when you select Northwire’s extrudable PTFE
• Chemically inert - Excellent resistance to oil, chemicals, and solvents
• Miniaturized cable design with high dielectric strength allowing for a thinner wall
• Low dielectric constant offers reliable electrical performance even with a thin wall
• Superior performance in abusive environments including cut, crush, and abrasion
• Low coefficient of friction ideal for high flex life applications
Due to the many benefits of these materials, fluoropolymers are used in a variety of industries, including:
Medical
- Because fluoropolymers have a low coefficient of friction, they are highly lubricious. This offers a soft and smooth feel for optimal patient and doctor comfort while also providing a surface that will not attract contaminants or bacteria. This feature also means it is well suited for high flex life applications, making it ideal for the numerous twists and turns that the cable could endure during surgery, for example.
- Resistance to chemicals and solvents means that cables designed with these materials will be wipe down resistant and will maintain performance even when exposed to hospital-grade cleaners.
Military, Aerospace and Defense
- Fluoropolymers offer a number of benefits to this industry due to its ruggedized nature. With resistance to extreme temperatures, cut, crush, abrasion, chemicals, and more it is hard to even imagine an environment that is too harsh for these materials.
- A low dielectric constant means superior electrical performance even when designed with a thin wall.
Transportation
- A low cold flow means minimal deformation at sub-zero temperatures. As a result, the transportation industry will benefit from an extreme temperature range on both ends of the spectrum, from high heat engine compartments to frigid aerospace applications.
- A high dielectric strength makes it possible to extrude a thinner wall, which means less material. This leads to a weight and space savings, two critical benefits in the transportation industry.
Industrial Automation
- That low coefficient of friction means these materials will hold up even in high flex life applications where the cable will be subjected to continuous movement, which can be particularly beneficial in industrial automation or even robotic environments.
- Knowing that cost can be a concern in this industry, the high dielectric strength and thinner wall means less material being used and a potential cost savings.
- Resistance to oil and chemicals also means these cables will maintain performance even when exposed to a variety of liquids in the industrial or manufacturing environment.
Benefits of Northwire’s Extrudable PTFE vs. Traditional Ram Extruded PTFE
As mentioned previously in this article, despite all of the amazing benefits, one aspect of PTFE that has been holding engineers and cable designers back from utilizing the material is the fact that it has had to be produced through a manufacturing process known as ram extrusion. This process of extrusion limits the quantities that can be produced and also results in a very inconsistent wall thickness. Enter Northwire… In May of 2019, Northwire released a PTFE with an enhanced way to process the material through a traditional screw extruder.
No Length Restrictions
Customers benefit from this more advanced way to process the PTFE conductor insulation and overall jacket material because unlike traditional PTFE, this option from Northwire is well-suited for high volume production and does not suffer from length restrictions. This means that Northwire can run the product continuously to meet the requirements of the customer and their end application vs. the limits of the extrusion process.
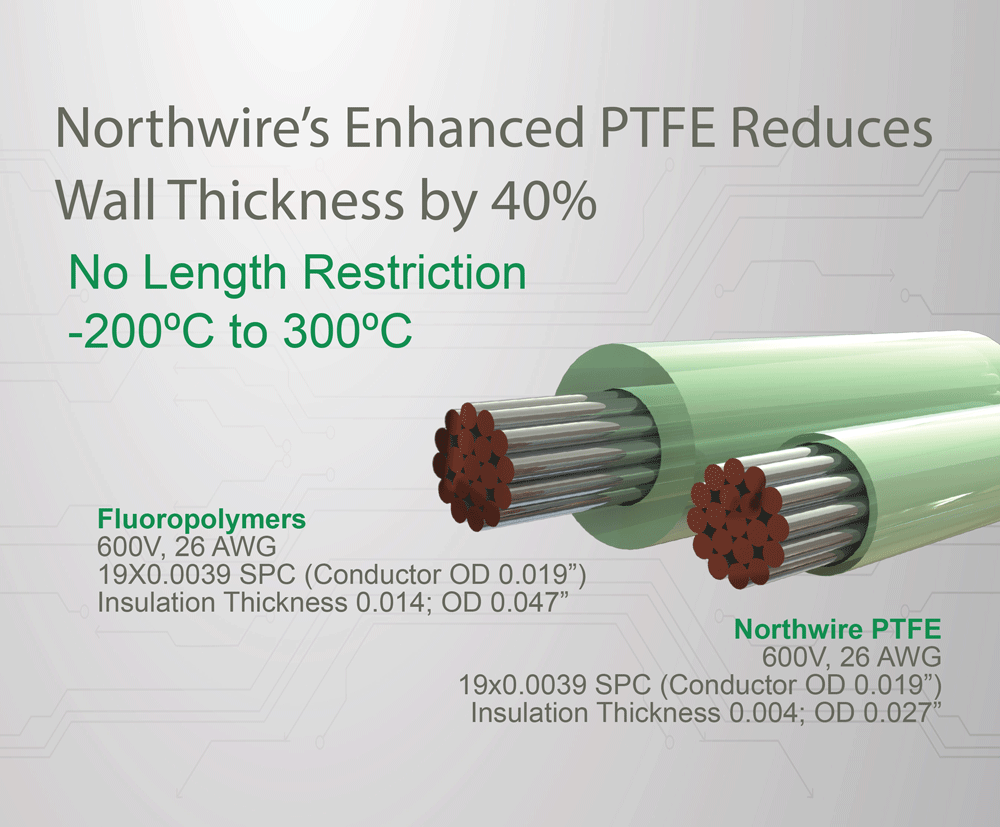
An Even Thinner Wall
This enhanced PTFE also offers superior dielectric properties. But wait a minute…we already said that fluoropolymers overall offer a high dielectric strength, which means cable and wire insulated with these materials can be designed with a thinner wall. That is true, however, it is also true that Northwire’s PTFE can be even thinner. It can offer a reduction of wall thickness of up to 40% compared to other fluoropolymers! That means space reduction, weight reduction, and potentially cost reduction! A low dielectric constant also means reliable electrical performance despite that thin wall.
Material Consistency
Consistency of the material thickness is another benefit of Northwire’s PTFE over the traditional ram extruded version. Because Northwire is extruding this new PTFE via a screw extruder, the wall thickness will remain constant and will not vary like it does when ram extruded. This can offer customers peace of mind and eliminate any issues related to sections of the cable and/or wire that may have too much material or too little material, which can result in spark outs. A spark out is when the insulation material is too thin or perhaps there is a gap in the material, so the conductor is exposed.
Extreme Temperature Resistance
Finally, one of the more common reasons that an engineer would consider a fluoropolymer would be because of the high temperature requirements of the environment of their end application. Most fluoropolymers are rated up to 260°C, but the great thing about this new PTFE by Northwire is that it can perform in environments up to 300°C. Those additional 40 degrees of temperature range could make a big impact when performance is imperative in extreme environments. Additionally, an extremely low cold flow means that the material has minimal deformation at sub zero temperatures making it ideal for applications in extreme cold such as the aerospace industry.
With a myriad of benefits, it is clear why fluoropolymers are a popular choice among engineers and cable designers alike. With extreme temperature performance, chemical inertness including resistance to oil and solvents, superior electrical characteristics and a low coefficient of friction, these materials are well suited for applications in a variety of industries especially those in rugged environments. With multiple material options available, cable design engineers are ready to partner with customers to better understand their specific end application needs to ensure the correct material is selected and designed into the cable solution. If customers have been avoiding PTFE due to the ram extruded limitations of length restrictions and inconsistent wall thickness, it may be time to take a closer look at Northwire’s PTFE which does not suffer from those same limitations.
So, whether you are at the very beginning of your cable design project with barely a napkin sketch or you have a current design that could benefit from a second look and perhaps a redesign to improve performance or potentially offer a cost reduction, consider partnering with one of Northwire’s Cable Design Engineers to get a better understanding of the various fluoropolymers offered including PTFE.